How to choose the right type of hammer mill grinder?
When you want to buy a hammer mill grinder to process wood and crops, you can ask yourself the following questions for reference.
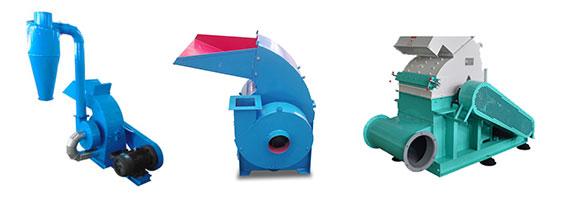
What raw materials do you want to crush?
- To crush grain feed, you can choose hammer mill with the feed hopper on the top.
- To crush wheat and bran cereals, you’d better choose disc mills.
- To process mineral feed like shells, you can choose non-sieve grinders.
- The pretreatment of mixed feed requires small and adjustable particle sizes, you should choose special type of non-sieve grinder.
- If you want to crush different kinds of materials, such as grains and crop straws, you can choose tangential feeding hammer mill grinder.
What's you required production capacity?
Generally, on the instruction and nameplate of the hammer mill grinder labels the capacity rating. But you should be clear that the rated capacity is under standard condition. For example, the standard of grain hammer mill is when the moisture content is around 13%, the screen mesh diameter is 1.2mm. This is the smallest screen mesh with low production. You should consider these factors when buying.
The production capacity of the hammer mill you choose should be a higher than your demand. Once the production drops due to hammer wear or air duct leakage, the production capacity would decrease.
What’s the power of the hammer mill grinder?
On the instruction and nameplate of the hammer mill grinder usually labels the rated power of the electric motor. It is not a fixed number but a certain range. The required power varies with different raw materials. For example, under the same working condition, the required power for crushing sorghum is 1 time more than that of corn. Besides, with different size of screen mesh, the load of the hammer mill are varied.
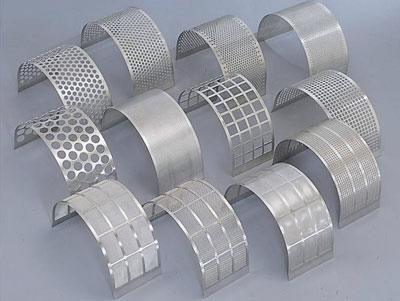
How much electric power does your hammer mill consume?
In some areas, the government stipulated the least energy efficiency ratio for production. For example, when grinding corns with 1.2mm screen mesh, the output per KWH shall not be less than 48 kg. Nowadays, most hammer mills have their energy efficiency over the required level. Some superior hammer mills have achieved 70-75kg per KWH.
How are your raw materials discharged?
The crushed materials are discharged in 3 ways: self-weight, negative pressure suction, and mechanical transport. Small hammer mills usually adopt self-weight discharge method. Middle-scale type are usually equipped with negative pressure suction device, which can absorb moisture from the materials. To lower the moisture content of raw materials will increase the grinding efficiency by 10-15%, lower the dust degree in the crush chamber, and facilitate storage.

How mush dust and noise the hammer mill generates?
In a feed pellet plant, most dust and noise come from the hammer mill. You must take these sanitation factors into consideration. If you have chosen hammer mills with high noise and dust generation, you have to take noise and dust prevention method to improve the working environment.
What affects the production efficiency of hammer mills?
To choose the right type of hammer mill grinder, the most important parameter is the production efficiency. Different hammer mills varies a lot in production efficiency, which is affected by the following factors:
Raw material moisture content
Crop straws with high moisture content has high tenacity and hard to crush. The moisture content would increase the viscosity of the raw materials and reduce their fluidity, so as to lower the output speed and the production efficiency.
The diameter of the crushing chamber
Reasonable crushing chamber size can increase the working efficiency of hammer mill. The diameter of crushing chamber should adapt to the raw materials and the sieve mesh size.
Spindle speed
Within certain range, the higher the spindle speed, the higher the production efficiency. But once the spindle speed surpass the limit value, the production efficiency would drop. In the empty return stroke, if the spindle rotates too fast, the hammers will swing at high frequency. The raw materials have very short time to pass, so the crushed materials cannot be expelled successfully, and block the crushing chamber. By contrast, low spindle speed would cause the slow swing of hammers, so the raw materials can’t be fully crushed.
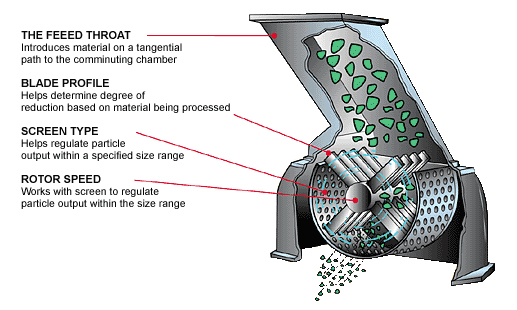
Routine maintenance
Good operating condition is the premise of high production efficiency. As a crushing equipment, the high working intensity will accelerate the abrasion of core parts. Therefore, the user should inspect and maintain the hammer mill regularly, so as to ensure the production efficiency and prolong the working life.
Standardized operation
The operator of the hammer mill need professional training, and have a comprehensive understanding of the equipment. Operating the hammer mill in accordance with regulations can ensure the safety of labors and the equipment.
We receive enquiries in English, Español (Spanish), Русский язык (Russian), Français (French) and العربية (Arabic). Our professional team will reply to you within one business day. Please feel free to contact us!