rotary dryer
Rotary dryer for pellets is widely used in industry to reduce or minimize liquid or moisture content of the material with heated gas. Rotary dryer is composed of a large, rotating cylindrical tube, usually supported by concrete columns or steel beams. Biomass materials go through the rotary dryer for pellets can improve biomass fuel efficiency of 5-15% and lower down emission.GEMCO rotary dryer for pellets mainly has two types: energy-saving three-layer rotary dryer and single-layer rotary dryer.
Pictures of Rotary Dryer
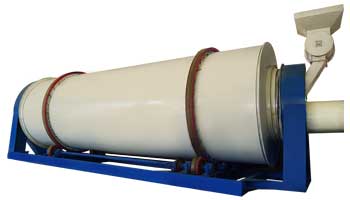
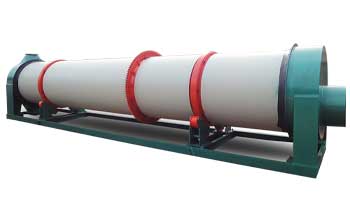
Technical Data of Rotary Dryer
Model | Diameter (mm) | Length(m) | Power(kw) | Speed of rotation (r/min) |
---|---|---|---|---|
HZG6 | 600 | 4,5,6,7,8 | 3-5.5 | 3-20 adjustment |
HZG8 | 800 | 4,5,6,7,8,9,10 | 5.5-7.5 | 3-20 adjustment |
HZG10 | 1000 | 6,7,8,9,10,11,12 | 5.5-7.5 | 3-20 adjustment |
HZG12 | 1200 | 6,8,10,12,14,16 | 7.5-11 | 3-20 adjustment |
HZG15 | 1500 | 8,10,12,14,16,18 | 11-15 | 3-20 adjustment |
HZG18 | 1800 | 8,10,12,14,16,18,20 | 15-18.5 | 3-20 adjustment |
HZG22 | 2200 | 10,12,14,16,18,20,22,25 | 18.5-22 | 3-20 adjustment |
HZG24 | 2400 | 12,14,16,18,20,22,25 | 22-30 | 3-20 adjustment |

How does the rotary dryer work?
For the three-layer rotary dryer, its working principle is as following: The cylinder of rotary dryer is slightly inclined from horizontal, thus making material move from the feeding inlet to the discharge end under gravity. The material is fed by feeding device into the inner layer of the revolving cylinder where forward flow drying is realized. The material is repeatedly shoveled and dispersed by lifting plate to do heat exchange in screw movement forward. Then the material moves to another end of the inner layer and enters the middle layer, where counter flow drying is realized, and the material is windowed repeatedly and makes its way two steps forward and one back. During this process, the material fully absorbs the heat given by both the inner and middle revolving cylinder, and meanwhile the drying time is extended, which ensures material is completely dried. The material moves to another end of the middle layer and falls into the out layer, where the material makes its way in form of rectangle multiple chains, and the finished drying material moves rapidly and is discharged out of the drum by heat wind, while the material with high moisture content cannot move fast because of deadweight, and is fully dried inside the rectangle lifting plate.
As for the one-layer rotary dryer, the damp raw material is put into the dryer on one end and is turned over by the string-up rake inside the cylinder and distributed uniformly in the dryer for full contact with the countercurrent hot air. It speeds up heating and mass drying processes. When drying, raw material is moved by stirring rake with a gradient of hot air. It passes through the drying region to a star valve which discharges the finished product.
Advantages of Rotary Dryer- Both the single-layer rotary dryer and the three-layer rotary dryer manage to match the characteristics of products. Heating options include steam gas, oil, or thermal oil.
- With an equal production, both the single-layer and three-layer are characterized by less room taking, easy for transportation and installation.
- For the three-layer rotary dryer, it is sufficient in heat exchange: the heat exchange between the material and the heat air is realized by reciprocal and cross motion in the direction of forward flow, counter flow and again forward flow, with long time of heat exchange, and the water evaporated from the material inside the inner revolving cylinder is directly exhausted by the fan, therefore the heat utilization rate is high.
We receive enquiries in English, Español (Spanish), Русский язык (Russian), Français (French) and العربية (Arabic). Our professional team will reply to you within one business day. Please feel free to contact us!