What's the compression ratio of wood pellet machine?
In biomass pellet production, the compression ratio of pellet mill die should adapt to specific materials. The compression ratio of pellet mill die is determined by the hole size, thickness, the taper of the bell mouth, the material, and the hardness.
The die hole sizes are usually 6mm, 8mm, and 10mm. They are determined by the diameter of the die, the raw material composition. If the hole sizes are larger than 10mm, they are biomass briquette machine.
The thickness of pellet mill die have great impact on the molding effect. If the dies are too thick, the molding time will be long, the density of wood pellets will be high, and the extrusion strength is high. On the other hand, If the dies are too thin, they will be easy to break, the wood pellet density is low, the extrusion temperature is low, the production is high but the molding rate is low.
What does the compression ratio mean?
The compression ratio of pellet mill die varies with the raw materials. For example, the compression ratio of poplar is 1:6, pine wood is 1:7, hardwood is 1:5, wood shaving is 1:5.5, corn straw is 1:8. The harder the materials, the lower the compression ratio; the more fluffy the raw materials, the higher the compression ratio. In other words, fluffy raw materials are easier to mold, because they contain more fibers.
What does the ratio 1:6 mean? 1 refers to single hole diameter, 6 refers to effective hole size. The effective hole size is the single hole diameter multiply by effective hole length. For example, the compression ratio of poplar wood is 1:6. If the hole diameter is 8mm, the effective hole size will be 48.
The compression ratio determines the molding effects of wood pellets. If you don’t have requirement on the molding rate, you can choose a pellet mill die with low compression ratio, so that you can increase the productivity, and reduce the abrasion of pellet mill die and roller.
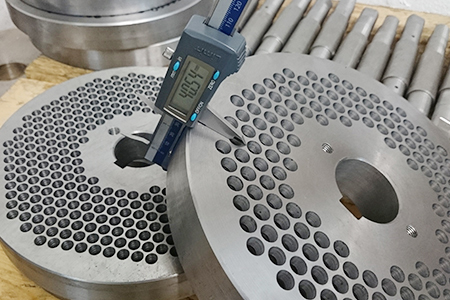
How to choose a suitable pellet mill die?
Choose high-quality pellet mill die from reliable manufacturers. Choose appropriate die hole form, opening ratio, and compression ratio according to the hardness of raw materials. Under the premise of ensuring the strength of the ring mold, try to increase the opening ratio of the die. For some kinds of materials, under the condition of ensuring reasonable compression ratio, the die is too thin, so that the strength is not enough, and the explosion will occur in production. The mold phenomenon, at this time should ensure the thickness of the ring mold and increase the pressure reduction hole under the premise of ensuring the effective length of the die hole.
The compression ratio of pellet die refers to the ratio of effective hole length and the least hole diameter. It is an indicator of the extrusion force of the wood pellet machine. The higher the compression ratio. The larger the compression ratio, the harder the extruded wood pellets.
- For dies with straight holes, the effective length is equal to the thickness of the ring die, while the minimum diameter is the diameter of the die hole.
- For releasing step holes and external cone holes, the effective length is equal to the ring die thickness minus the length of releasing holes and external cone holes, the diameter is measured at the narrowest part of the hole.
- For compressed stepped holes and internal tapered hole, the effective length is the thickness of the ring die, the diameter is measured at the narrowest part of the hole. But in these holes, its compression ratio is not the same as the situations above.
Roughness is also an important indicator of the quality of the ring mold. At the same compression ratio, the greater the roughness value, the greater the extrusion resistance of the wood pellets, the more difficult the discharge is, and the excessive roughness also affects the quality of the particle surface. A suitable roughness value should be between 0.8 and 1.6.
We receive enquiries in English, Español (Spanish), Русский язык (Russian), Français (French) and العربية (Arabic). Our professional team will reply to you within one business day. Please feel free to contact us!